
The Project
Cavendish Farms processes potato products of many different cuts and forms. To control the sugar content, the fries are first removed of natural sugars in a blancher, and then dextrose is added through a dip tank solution. The dextrose concentration of the dip tank must be measured to ensure proper sugar content for frying; uniform coloration in the fries is important at Cavendish Farms for their product to meet company and customer standards. The current system they have for measuring sugar content is periodic manual sampling which is taken to their lab where a bench-top YSI biochemistry analyzer measures small chemical reactions in a test tube to give the sugar concentration. This process causes a 15-minute delay for sugar adjustments and is often skipped. Cavendish Farms is looking for an in-line measurement system to identify the amount of sugar in the French fry processing line at the second of their plants in New Annan, PE.
Problem Statement:
The current testing method for sugar content monitoring in Cavendish Farms’ French fry processing line requires manual sampling and lab analysis, which causes lag and inaccurate adjustments. As such, an in-line measurement system is required to provide real-time readings of sugar content in the blancher and dip tank
Attempted Solution:
Cavendish Farms had already attempted to use a UR62 refractometer before the commencement of the project. The UR62 was capable of measuring sugar levels within 12% of the YSI measurements. However, the sensor probe is prone to starch build up which covers the lens of the refractometer and causes inaccurate data. In addition to the starch build up, the UR62 suffered water damage from the cleaning processes at Cavendish Farms, which rendered the refractometer out of service. As such, Cavendish Farms needs a new sensing device which addresses the flaws in the UR62 and has improved accuracy.

The Client
Cavendish Farms is a company under the J. D. Irving brand established in 1980 after buying the C.M. Maclean processing facility on Prince Edward Island. They supply potato products of many different cuts and forms to businesses in North America, with processing plants in New Annan, PEI, as well as plants in Jamestown, North Dakota; Lethbridge, Alberta; and Wheatley, Ontario. Cavendish Farms is vertically integrated, so they control their product from farm and crop management, to storage and processing, and packaging and transportation [1]. Cavendish Farms is focused on satisfying their customers with the highest standard of quality food and service.
[1] Our Story - Cavendish Farms. [Online]. Available: https://cavendishfarms.com/en/our-story/. [Accessed: 18-Sep-2018].
​

The Team: Tater-Dactyl Sugar Control
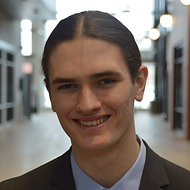
Lucas Gallant
Team Lead​

Patrick Walsh
Project Manager​

Hammad Ahmed
Communication Lead​

Hamood Dalbah
Technical Lead​